
The nail heads might put a slight blemish in the finished surface, but its nothing that a light sanding wont take care of. Then you can coat the whole board and lay it with the bottom resting on the nail heads. One way to do this is to take a piece of scrap ply and put a few nails into it. That is, unless you come up with a system that lets the board breathe while it dries. Just be sure to use a good push stick.Ģ- You would need to let the board dry before coating the other side. I would not recommend doing that as your first cut on a tablesaw, but once you are comfortable with the machine, you should be in good shape to try it. And with some experience and the right push sticks, that cut is relatively safe. But in cases where you need a consistent sized cut, it just makes more sense to do it that way. Well first off, congrats on the mini-woodworker! Getting any sleep lately? :)ġ- I agree that that type of cut is not ideal. I have a splitter on one table saw and think it is a good idea for ‘rough’ or green wood. Like you and ‘Norm’ I don’t use a blade guard although if I was making a video I would that was because it is easier for the camera to see the cut. Drilling and placing the magnet takes a little longer. I can cut one out on the bandsaw in under a minute so I don’t go to that kind of trouble. It is usually made out of plywood and I’ve seen guys that make the sacrificial notch so that it is replaceable.
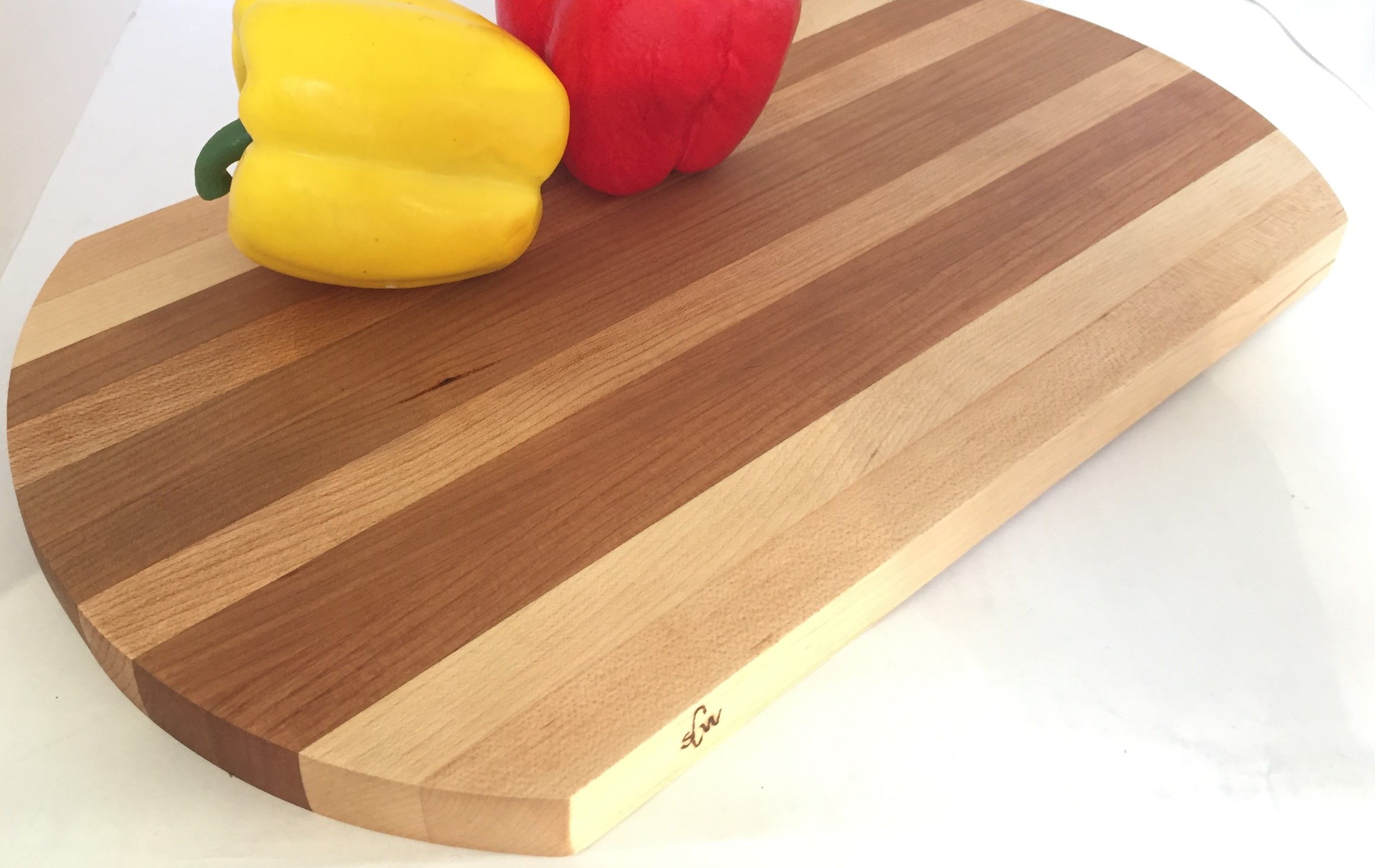
( ) I make a couple of these a year and usually embed a magnet in the side to that it is easily attached to the table saw. The push stick you were using could only be described as ‘weenie’. I always realize that it is not a safe cut and I brace myself and use a good push stick. Having said that, I done it a number of times. ‘Never cut cross grain against the fence.’ (Try that on Google and see how many hits you get.) In every table saw book of safety procedures the tell you never to do this. The cut you made today on the glued up layers of the cutting board is very dangerous. I subscribe to your podcast through iTunes and enjoy them.

So instead of just cutting trimming the length and width and calling it a day, I decided to have some fun with it. It turned out to be far too large for our kitchen. Once of my first cutting boards was a very large board made of purpleheart and birch (left). But what you may not know is the fact that this design came about almost by accident. I think its safe to say this is the video that launched a thousand cutting boards! So you may already be very familiar with this design. I never thought when I made this video that so many folks would find the plan useful and make their own.
#Falling blocks cutting board how to
I’ll also discuss how to maintain the board and keep it looking fresh for years to come! I’ll cover the preparation and construction of the board itself, as well as the various finishing options available. And if you are relatively new to woodworking, this is a great project to hone your milling, glue-up and tablesaw skills. A custom cutting board makes a great gift and many woodworkers make them in batches every Holiday Season. Im not sure if its the “back to basics” simplicity or just the fact that it is one of the most useful projects a woodworker can make, but something keeps bringing me back for more. One of my favorite woodworking projects is a butcher block end-grain cutting board.
